La Révolution Industrielle des Imprimantes 3D |
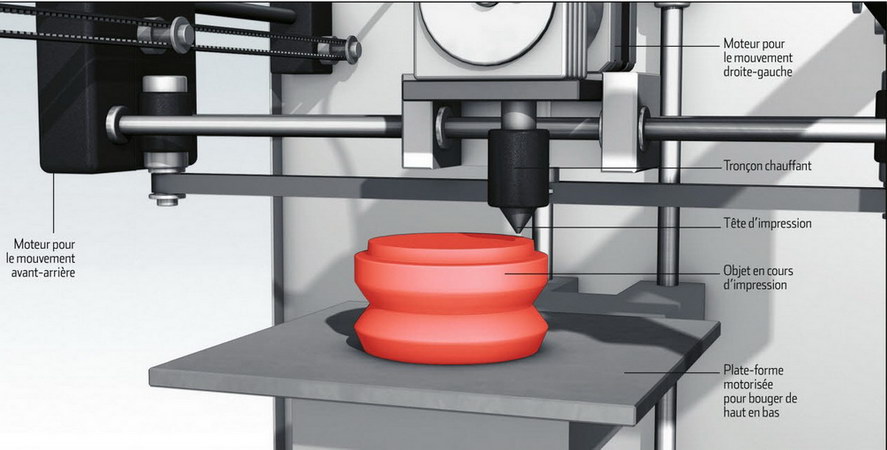
Que ce soit pour la conception, le prototypage ou la production d'objets, les imprimantes 3D changent aujourd'hui radicalement la donne. Avec elles, toutes les audaces deviennent permises, à moindre coût et en un temps record. Décryptage d'une révolution industrielle qui n'en est qu'à ses débuts.
JARGON : Les imprimantes bureautiques déposent sur du papier des micro-gouttelettes d'encre liquide ou une très fine poudre de pigments qui sera fondue par un laser. Quant aux imprimantes 3D, elles déposent, couche après couche, soit du liquide (résine, cire...) qui sera durci ou séché, soit de la poudre (plastique, métal...) qui sera fondue et solidifiée.
REPÈRE : L'impression 3D naît en 1986 : l'Américain Chuck Hull fait breveter un procédé consistant à déposer une fine épaisseur de résine polymère liquide, solidifiée couche après couche par rayonnement ultraviolet. Le procédé (la stéréolithographie par photopolymérisation) en inspira de nombreux autres, comme le dépôt de fil plastique par extrusion ou encore la fusion et le frittage sélectifs par laser.
C'est l'un des moteurs les plus attendus de l'aviation mondiale. Le LEAP - c'est son nom - s'annonce comme un petit bijou de technologie, voué à propulser les futurs Airbus A320neo et Boeing 737 MAX. Or, pour la première fois dans l'histoire de l'aviation, ses injecteurs de carburant (ces composants normalement constitués d'une vingtaine de pièces en alliage chrome-cobalt, qui n'ont absolument pas le droit de tomber en panne ne seront ni coulés dans un moule de fonderie, ni patiemment usinés au micromètre près à partir d'un bloc de métal. Ils sortiront directement... d'une imprimante 3D !
Une prouesse, qui prouve que l'impression 3D, née il y a plus d'un quart de siècle (voir "Repère"), entre aujourd'hui dans son âge d'or. Et qu'elle ne se limite pas à la fabrication de coques de smartphone, figurines de superhéros ou autres objets simples en plastique, réalisés avec des imprimantes basiques. La révolution des objets n'est plus seulement commerciale, elle est industrielle. Qu'il s'agisse de pièces professionnelles de haute qualité ou de gadgets, le principe reste le même : un objet est d'abord dessiné en volume sur ordinateur, grâce à un logiciel de conception 3D. Ce modèle numérique est ensuite découpé en fines tranches, puis envoyé à l'imprimante, qui va superposer les tranches de matière constituant l'objet, couche après couche, de sa base à son sommet. D'où l'appellation "fabrication additive", par "addition" de matière, par opposition aux traditionnelles opérations d'usinage, qui extraient l'objet d'un bloc brut par enlèvements successifs de matière.
Si l'impression 3D décolle aujourd'hui dans l'industrie, c'est parce que les technologies ont profondément évolué. Restreinte à quelques types de plastique à ses débuts, elle s'ouvre à de plus en plus de matériaux. En particulier les métaux, via l'utilisation de lasers et de faisceaux d'électrons qui atteignent des températures de plus en plus hautes (jusqu'à 2000°C), ce qui permet de fondre toutes sortes de poudres métalliques (acier, aluminium, or, chrome, cobalt, "superalliages" nickel-chrome, titane...), lesquelles ferment les couches successives des objets imprimés. Sans oublier une gamme de plus en plus large de plastiques et de céramiques, du verre, du plâtre, de la cellulose et même du chocolat ou encore plus sidérant - des cellules vivantes ! La qualité de finition a également fait des progrès décisifs. La résolution des pièces imprimées peut désormais atteindre celle que l'on trouve couramment en usinage traditionnel, soit 16 micromètres pour l'impression par dépôt de cire, très prisée en joaillerie.
ENCORE PLUS RÉSISTANTS
Même leur solidité n'a plus grand-chose à envier aux standards classiques... Au contraire ! "Nous avons été surpris de constater que les pièces imprimées en métal sont parfois plus résistantes que les pièces de fonderie", explique Jon Meyer, de l'EADS Innovation Works, la cellule recherche et développement de l'avionneur européen. Notamment parce que leur forme est adaptée aux contraintes qu'elles devront supporter - ce qu'il serait impossible d'obtenir autrement. C'est que la fabrication additive révolutionne la conception même des objets, en s'affranchissant de ses limites traditionnelles. Dans le cas des pièces de fonderie, le métal est coulé à l'état liquide dans un moule, puis refroidi ; la forme de l'objet ne doit pas empêcher le démoulage. Quant aux pièces usinées, extraites d'un bloc de métal, le perçage (utilisé pour enlever de la matière jusqu'à obtenir la forme voulue) ne peut se faire qu'en suivant une ligne droite (voir infographie). Avec une imprimante 3D, plus de forme à extraire d'un moule, plus de trou à creuser : les espaces vides apparaissent tout simplement là où la matière n'a pas été déposée. "Ce mode de fabrication libère l'imagination des designers", souligne Prabhjot Singh, directeur du laboratoire de fabrication additive de General Electric. Un aperçu ? Un avionneur m'a demandé récemment d'imprimer une pale de moteur dotée d'un canal de refroidissement en spirale qui épouse parfaitement la forme de la pale, témoigne Juan Franco, PDG d'Eichenberger, spécialiste suisse du frittage sélectif par laser, l'une des technologies d'impression 3D. Cela aurait été très complexe, voire impossible à faire autrement".
Autre exemple : "L'impression 3D permet de travailler avec des alliages difficiles, ou qu'on ne peut carrément pas utiliser en fonderie, comme ceux à base d'aluminium et de magnésium renforcés au scandium. Cela ouvre de nouvelles possibilités, que nous commençons à peine à percevoir", estime Jon Meyer. Conséquence : "La complexité d'une pièce n'influe plus ni sur le temps de fabrication, ni sur le coût. Seul compte le volume imprimé, c'est-à-dire la quantité de matière utilisée", résume Alex Gryson, designer chez Sculpteo, un prestataire français de services d'impression 3D pour particuliers et professionnels. Des formes libérées, des matériaux inédits, une économie de temps et de matière inespérée jusqu'ici : l'industrie ne pouvait rêver mieux. Et de fait, elle est bel et bien en train de vivre sa révolution 3D. Avec certains secteurs particulièrement intéressés, pour au moins trois bonnes raisons.
FACILITER LE PROTOTYPAGE
La première, c'est le gain de temps. L'automobile et la joaillerie, les premiers, se sont emparés de l'impression 3D pour leurs prototypes - l'équivalent du brouillon pour les industriels. Objectif : réaliser vite, et à moindre coût le modéle d'un futur produit pour vérifier sa conformité avant de lancer sa production en série. "Sur les showcars que l'on voit dans les salons automobiles, 90 % des pièces de petite taille sont imprimées en 3D", révèle Clément Boutet, responsable du showroom parisien de Multistation, un revendeur d'imprimantes 3D. De quoi économiser plusieurs semaines à plusieurs mois, le temps habituellement nécessaire pour fabriquer les équipements de production, comme les moules. L'américain Chevrolet a lui aussi utilisé deux techniques d'impression 3D (la stéréolithographie et le sélectif par laser) pour sa nouvelle berline Malibu. "Cela a permis de réaliser en quelques jours des maquettes qui, auparavant, auraient pris plusieurs semaines de sculpture d'argile", détaille le constructeur. Idem pour les maquettes de bâtiments en architecture.
Deuxième explication au ralliement de nombre d'industriels à la 3D : l'économie de matière. Les rebuts (copeaux, rognures, ébarbures...) produits par l'usinage peuvent en effet représenter jusqu'à 80 % de la matière utilisée. En ne la déposant que là où c'est nécessaire, la fabrication additive optimise de façon inédite le rapport poids-résistance des objets produits. Une capacité qui intéresse au plus haut point l'aéronautique, toujours à la recherche d'allègement. "Le gain peut atteindre 60 % pour des pièces telles que des charnières de capot moteur, explique Jon Meyer. On évite aussi les déchets de métaux onéreux et difficiles à usiner, comme le titane ou les alliages de nickel". Un constat partagé par GE Aviation, co-concepteur de l'injecteur de carburant du futur moteur LEAP. Avec l'impression 3D, la pièce (présente en 19 exemplaires dans chaque moteur) est 25 % plus légère, et sa longévité est plus de 5 fois supérieure.
Dernier atout : la capacité de l'impression 3D à fabriquer des produits sur mesure sans faire exploser les coûts. Il suffit de modifier le fichier 3D sur ordinateur pour intégrer des spécifications. Des constructeurs automobiles haut de gamme comme Bentley réalisent des pièces personnalisées (tableau de bord, intérieur...) selon les desiderata de leurs clients fortunés. L'industrie s'offre ainsi ce qui était jusque-là une contradiction : du sur-mesure... en série ! Nul besoin d'être un VIP pour profiter de ce nouveau mode de conception des objets, au plus près des besoins de l'utilisateur. Ainsi, les prothésistes y ont de plus en plus souvent recours. L'idée ? Scanner la partie du corps où sera insérée la prothèse, dessiner un modèle numérique, puis l'envoyer à l'imprimante. Dès 1995, les prothésistes dentaires ont commencé à imprimer des prothèses en acier, puis en alliage chrome-cobalt, en titane et en céramique (zircone). Les fabricants de prothèses auditives, dont la forme doit être adaptée au conduit auditif du patient, ont eux aussi profité de l'opportunité : plus de 60 % de la production mondiale est aujourd'hui fabriquée de la sorte.
Ces premiers succès dans le monde médical ont rapidement ouvert la voie à la chirurgie. D'abord pour la fabrication de guides chirurgicaux, ces structures servant à assister le chirurgien pendant l'opération, par exemple pour l'aider à respecter la position et l'angle de perçage lors de la pose d'une vis. Depuis les années 2000, l'utilisation s'est étendue à la réalisation de tout type de prothèse personnalisée : implant cochléaire, lentille de contact, prothèse de genou ou de hanche, exosquelette... En 2012, la première mâchoire inférieure complète imprimée en titane poreux a été implantée sur une patients de 83 ans. Début 2013, une équipe de l'université du Michigan (États-Unis) a fabriqué sur mesure, à partir d'un scanner, une attelle pour la trachée d'un bébé souffrant d'un affaissement des voies respiratoires. En octobre, le premier larynx artificiel posé chez l'homme par une équipe des hôpitaux universitaires de Strasbourg avait, lui aussi, été imprimé en 3D...
DE L'ENCRE À BASE DE CELLULES VIVANTES
Encore plus fort : des chercheurs commencent à imprimer en 3D des supports (par exemple, une forme d'oreille en collagène) sur lesquels pourront croître des cellules épousant la forme imprimée. Et en février 2013, des médecins de l'université Cornell (New York) ont annoncé avoir imprimé un premier pavillon d'oreille fonctionnel. En juin, se sont des chercheurs du Massachusetts Institute of Technology qui ont mis au point, un matériau comparable à de l'os humain. L'impression en 3D simultanée de deux polymères (l'un résistant, l'autre souple), selon une organisation spatiale calquée sur celle des os, a donné naissance à un échantillon de quelques centimètres aussi résistant que l'os humain, ouvrant des perspectives inédites dans la chirurgie réparatrice. Certains laboratoires essaient d'aller plus loin. Ils espèrent réussir à créer des organes en imprimant... des cellules vivantes. En particulier des cellules souches, capables de se transformer en tout type de cellule humaine. Mises en solution dans une "bio-encre", ces cellules sont placées dans une buse qui, comme dans une imprimante à jet d'encre, les éjecte sous forme de spray pour recréer le modèle voulu. Placées dans de bonnes conditions de croissance et de stimulation, elles se développeront pour former un rein, un foie, peut-être un jour un cour. Du moins en théorie. Quelques laboratoires parviennent pour l'instant à fabriquer des fibres musculaires et des organes "simples" comme de la peau. Une start-up californienne, Organovo, crée des tissus vivants semblables, selon elle, à ceux du foie.
En 2011, l'équipe d'Anthony Atala, directeur du Wake Forest Institute pour la médecine régénérative (États-Unis), a annoncé avoir fabriqué un "prototype" de rein grâce à une technique d'impression 3D. Mais ce "facsimilé" n'est pas fonctionnel, car les chercheurs ne savent pas encore imprimer l'inextricable réseau de minuscules vaisseaux sanguins dont les organes ont besoin pour vivre et fonctionner. Les premiers organes fonctionnels imprimés en 3D sont espérés pour 2025. Certes, malgré les extraordinaires progrès de ces dernières années, les fabricants ont encore du pain sur la planche. "Les limitations actuelles restent la vitesse d'impression, la quaiité de finition, le manque de standards et de méthodes de qualification des pièces imprimées, l'absence de méthode fiable pour prédire les déformations techniques... Et bien sûr la limitation de taille des objets - 1 m pour les polymères, 40 cm pour la métal", note Prabhjot Singh. L'avenir de l'impression 3D n'en demeure pas moins assuré. Econolyst, société britannique de conseil dans le domaine de l'impression 3D, estime que le marché devrait atteindre 8 milliards de dollars à l'horizon 2020, contre 2,2 milliards en 2012.

Et le meilleur reste à venir. "Il y a probablement des possibilités que nous ne soupçonnons pas encore, pronostique Jon Meyer. Plus les ingénieurs s'approprieront ces techniques, plus ils auront d'idées sur la façon de les exploiter". D'autant que des progrès ne manqueront pas de renforcer les "superpouvoirs" des imprimantes : une partie des brevets protégeant ces technologies tombera dans le domaine public cette année, ce qui permettra à tout fabricant de s'en emparer et de repousser leurs limites actuelles. Des évolutions sont également attendues dans les logiciels de conception 3D. "Nous essayons de développer des programmes plus intuitifs et plus accessibles", explique Didier Cocherel, directeur de la zone Europe chez l'éditeur américain de logiciels Autodesk. Reste aux ingénieurs et aux designers à apprendre à débrider leur créativité pour exploiter au mieux tout le potentiel, présent et à venir, de ces incroyables machines.
P.-Y.B. - SCIENCE & VIE N°1157 > Février > 2014 |
|